Spencer's Book of Secrets...
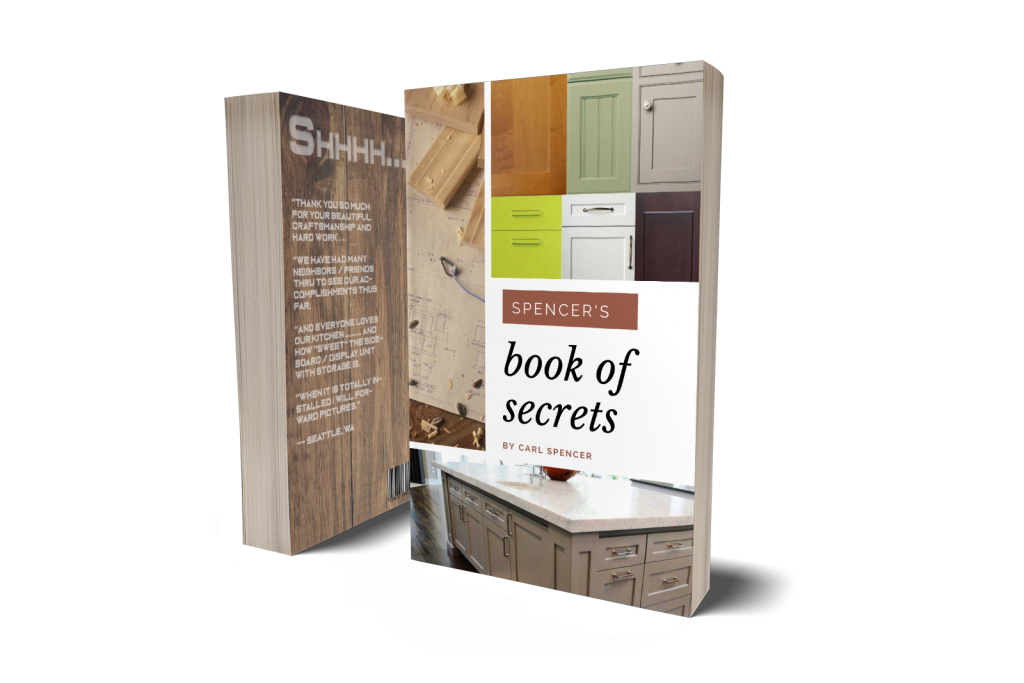
Don't tell our competitors!
Our “Book of Secrets” is our secret sauce…it’s our “original recipe.” It’s also what sets us apart from our competitors. More importantly, it’s why our customers continue to choose us for their custom cabinets and refer us to their friends and family.
There are a number of details that other cabinetmakers overlook that we don’t. Frankly, these are details that you likely haven’t considered, or details that haven’t been brought to your attention, that are important to the overall quality and longevity of your new cabinets.
Things like applying 50% more finish on the end grain at the bottom of your cabinets, or why it’s important to adjust the curing temperatures and times on your cabinet finish based on your specific wood. We mention these to you because (a) they have a significant impact on the quality and longevity of your cabinets (b) they are extremely difficult for our competitors to implement for systemic reasons.
Want to learn more? Read below:
“Thank you so very much for the cabinet door replacement, but mostly for all of the cabinets.
“They are so Beautiful.”
— Kirkland, WA
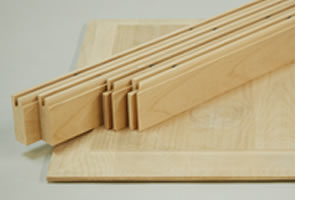
Why We Make Our Own Doors
Better Value: We don’t pay any outside door manufacturer’s profit margin, so you don’t have to either.
Aesthetics: All the doors come from the same batch of lumber as the cabinet box for perfect grain and color match. In contrast, wood for doors purchased by other companies can come from different parts of the country.
Design Flexibility: If you have a species or style in mind you don’t see in our showroom, we can typically make it for you anyway.
Tolerances and Quality: Our tight tolerances make styles like beaded-frame inset doors possible. We ensure each door meets a single, high quality standard. Outside door manufacturers have to maintain many different quality standards to suit the widely varying needs of their many customers.
Customer Service: If you need to replace a damaged door, we can normally make you a new one in one to two days. Most other companies take one to three weeks.
Expertise: We offer you all the advantages listed above because we have the requisite master cabinetmaking skills and experience. We have always made our own doors and we always will.
How We Make Our Shelves Truly Adjustable
We supply strong, steel-core adjustable shelf pins (see right example in photo) with our cabinets at no extra charge.
Most other cabinet companies use a cheap plastic clip, which is really great for the manufacturer because (a) it costs them less and (b) they can use it to secure adjustable shelves in the cabinet for shipping.
But the “advantages” of the plastic clip stop at the point of delivery. To move or remove the shelf, it takes one hand to depress the clip at the back of the shelf, another hand to depress the front clip — and yet another hand to move the shelf (we count three hands). Installers hate it because they typically have to remove the shelves to mount the cabinet properly on the wall. Homeowners hate it because (after breaking several) they simply give up and leave the shelves where the manufacturer or installer left them. Adjustable shelves? We think not.
Our steel-core shelf pin has superior shear strength for heavier objects and can be adjusted with one hand! In addition, we ship our adjustable shelves separately to save the installer time.
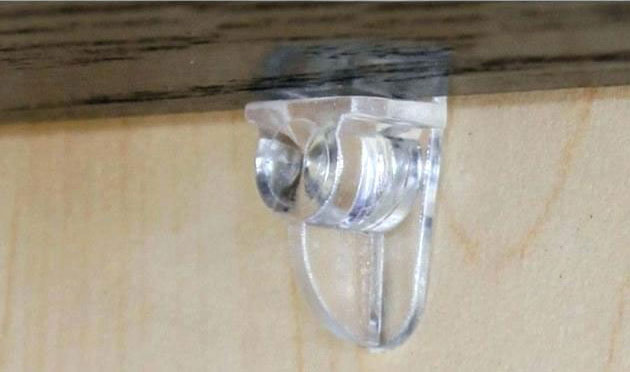
Strong, Steel-Core "One-Handed" Shelf Pins
“I included [a] picture to show you what a great job!
“As you can see . . . much neater than before.
“Thank you!”
— Everett, WA
“Thank you so much for your beautiful craftsmanship and hard work . . .
“We have had many neighbors / friends thru to see our accomplishments thus far.
“And everyone loves our kitchen ………. and how “sweet” the sideboard / display unit with storage is.
“When it is totally installed I will forward pictures.”
— Seattle, WA
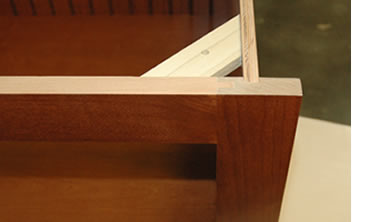
Extended Stiles are Standard at Spencer
(These are frame extensions, that help ensure a perfect, custom fit during installation).
How We Obtain the Best Cabinet Fit and Cleanest Appearance
We automatically (and at no extra charge) make the vertical frame members wider where your cabinets meet walls or other cabinets for three reasons:
1. It provides clearance for doors and drawers past door casing and other trim on the walls.
2. It provides clearance past pulls or knobs on cabinets, dishwasher doors or oven doors where the cabinets turn an inside corner.
3. It allows the installer to fit the cabinets precisely to the wall without resorting to ugly and expensive filler boards and the extra work they require.
It’s such a simple solution you have to wonder why some cabinet companies don’t offer it at all, and those that do charge extra for it! Of course, “frameless” brands of cabinets are stuck using myriad filler boards for obvious reasons. The remaining brands can’t handle such “non-standard” cabinets well. Except our flexible system can — so extended stiles are standard.
How We Reduce or Eliminate Finish Failure In Sink Areas
Most modern cabinet finishes are essentially waterproof on the front surfaces — a good thing in the kitchen and bath environments.
However, it is almost impossible to totally seal the end grain at the bottom of doors and face frames in a moving conveyor line finishing system used by most manufacturers. Not enough time in the booth is one problem. Poor edge coverage intrinsic with flat line spray systems is another.
It becomes your problem when water inevitably drips down the front of the cabinetry and hangs unnoticed for a long time under the bottom edge (see photo). Over time it wicks into the poorer finished end grain, swells the wood behind the finish, and causes the protective film to flake off.
The Spencer finishing system and proprietary technique apply 50% more finish specifically on the end grain for far greater water resistance right where you need it.
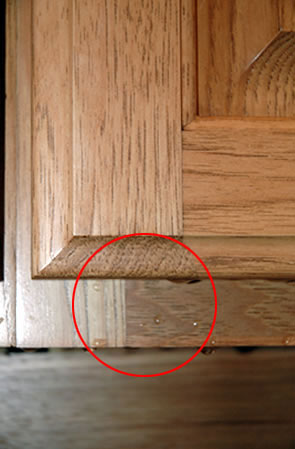
50% More Finish on Bottom Edges
“We are so very happy with the [Brazilian Cherry vanity and linen] cabinets you made for our master bath.
They are lovely!”
— Edmonds, WA
“I included [a] picture to show you what a great job!
“As you can see . . . much neater than before.
“Thank you!”
— Everett, WA
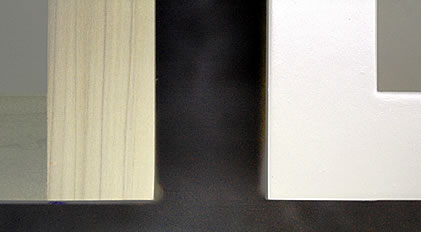
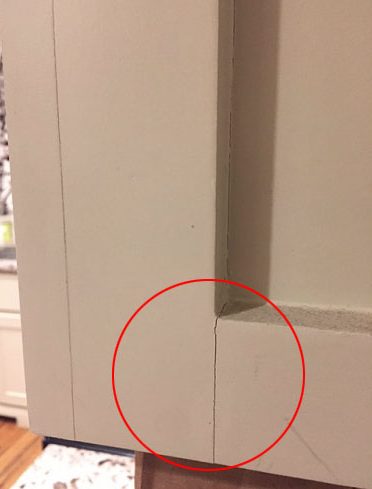
How We Reduce or Eliminate Paint Cracking at Joints
Surface flaws stand out even more with paint than they do with transparent stains and varnishes. Everyone knows you want to use a smooth wood for painted cabinets. In fact, most cabinetmakers believe this is the only criteria for species selection.
However, two other considerations are just as important: humidity-driven wood movement and hardness.
Humidity-driven wood movement: Wood expands and contracts significantly across its grain, but not much along its length. The horizontal rail of a face or door frame is always changing its width in conjunction with ambient humidity conditions and stretching the finish film back and forth. The adjacent paint on the vertical stile is moving in a 90° direction, shearing the paint and causing it to tear apart at the joint. Some of this is inevitable, but species selection can mimimize the degree.
How We Improve Finish Durability and Smoothness
Like all modern cabinet manufacturers, we cure our finishes in a large bake oven. Unlike most other companies, our oven is designed to bake each different finishing material at its ideal curing temperature and time.
No open spray booths, no dirty moving conveyor lines, and no wasteful open ovens for us! We leave the compromise curing conditions that are not ideal for any finish to our competitors.
First, you need a sealed, dust-free environment like ours with no conveyor or part movement during the entire process. Next, you need the correct “flash” time to let the bulk of the solvents escape and not bubble. Finally, you need just the right baking temperature and time.
Too low and the finish won’t be fully cured, especially “painted” finishes. Too high and it bubbles and feels rough. Our finishes always come out just right!
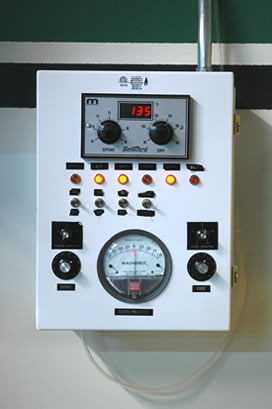
Ideal Baking Temperatures
“I just ran into [my neighbor] walking our dogs this morning and she said they [bought from] you also.
“Clearly your cabinets sell themselves!”
— Seattle, WA
How We Ensure the Best Quality and Service
Branded With Our Name
Every top drawer in our cabinets is branded with our logo (see photo).
We refer to this as the “signature” drawer for obvious reasons. The brand is inobtrusive, yet noticeable enough to serve several purposes:
As a marketing tool: Our brand helps people who see our existing cabinets and like them to find us.
As a customer service tool: Our brand directs people who need additional service from us to find us. For example, people have bought houses with our cabinets already in them and found us to provide additional matching cabinets (e.g., more laundry cabinets, entertainment centers, wet bars, etc.), or to professionally repair damage left by the previous owners, or just to add little things like drawer inserts, roll trays, or extra shelves.
As an accountability tool: Our brand is literally our last name. Not only our business reputation rides on the products we deliver, so does our personal reputation. We are very proud of what we make. There are many, many cabinet companies that don’t dare put their names on the products they deliver.