What is Premium Furniture Construction?
Simply put, what is under the countertop is as important as visible styling when it comes to the durability and longevity of your cabinetry.
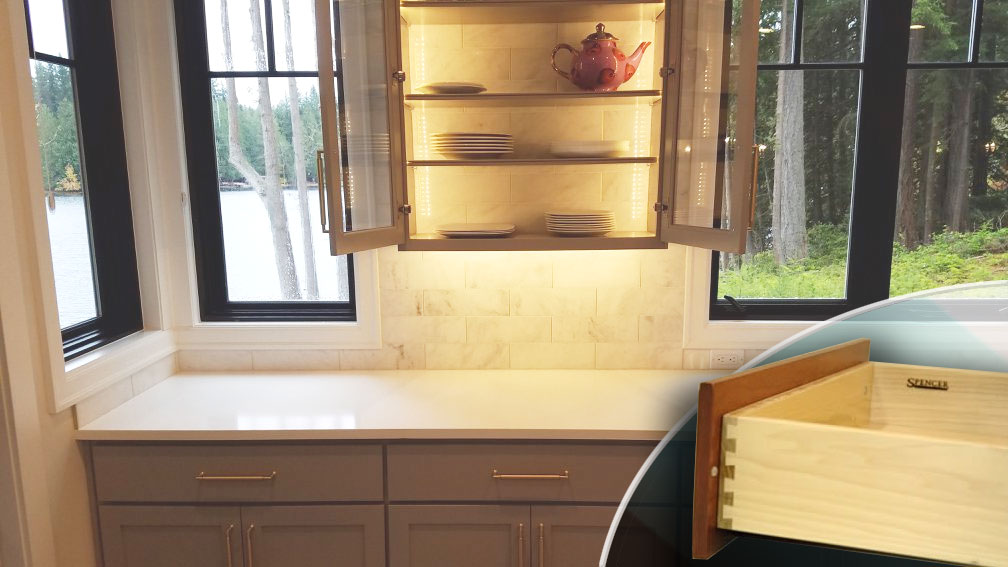
It turns out building cabinets using time-honored furniture-making methods doesn’t have to cost any more than throwing them together in large scale for the quick buck. Well-built cabinets simply look better and last longer . . . all in all, the best value. Below is a partial list of important furniture construction features typically not found in other cabinet lines, but standard with Spencer LLC:
Flush, Finished Ends
Other manufacturers ship their cabinets with an unfinished exposed end, then supply the installer with a finished panel “skin” to glue and nail into place under job-site conditions.
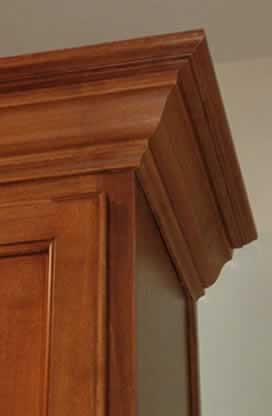
Flush, Finished Ends
Other manufacturers ship their cabinets with an unfinished exposed end, then supply the installer with a finished panel “skin” to glue and nail into place under job-site conditions. Their construction leaves a tell-tale ridge with a very visible clumsy joint down the front edge of every end cabinet.
Installers hate the extra work of applying these skins, not to mention having to notch this unsightly “scribe” ridge for trim moulding with a hand chisel. And you hate the not-quite-finished look to all the casework throughout your home.
Even if you can get flush, finished ends from another manufacturer, you will likely pay extra because it’s an abnormal process for them.
Spencer LLC’s production system is designed to build the professional furniture look of flush, finished ends as our normal process for no extra charge. We believe the cabinetmaker’s bench is the best place to build cabinets, not the job site. Also see wainscot panel ends.
Wainscot Panel Ends
We make our frame and panel wainscot cabinet ends the same way they have always been made by furnituremakers over the last several thousand year.
“Well, we love our new kitchen!!
“Every day I walk into the kitchen and think, ‘WOW! This is OUR kitchen!!’
“The cabinets are beautiful.
“I’m attaching some pictures so you can see the before and after:
“What a difference!!
“Thanks again for all your help.”
— Lynnwood, WA
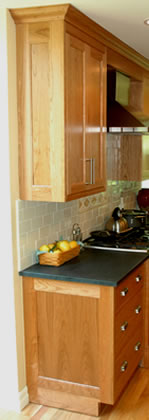
Wainscot Panel Ends
We make our frame and panel wainscot cabinet ends the same way they have always been made by furnituremakers over the last several thousand years — as the actual end panel built into the cabinet.
These are not the tacky plant-on doors or separately applied wainscot panels used by most “semi-custom” cabinet companies to simulate frame and panel ends, these are the real thing. And they don’t cost any more than the less attractive counterfeit wainscot panel ends, at least from us.
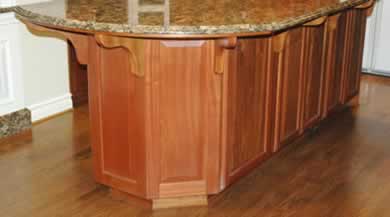
Sized to Fit
First, we personally field measure each room using laser technology to assure all cabinets fit neatly into place during installation (no extra charge).
“Thank you for the wonderful job on our custom cabinets.
“Your attention to detail and precise measurements were superb!
“We will have our future projects done with you and would recommend that anyone thinking of a remodel go with Spencer Cabinets.
“Your product is above and beyond.”
— Edmonds, WA
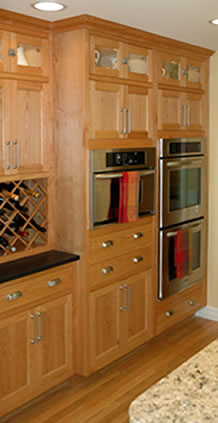
Sized To Fit
First, we personally field measure each room using laser technology to assure all cabinets fit neatly into place during installation (no extra charge).
Next, we make cabinets whatever size they need to be to optimize the function and esthetics of the room (no extra charge). Our manufacturing system has been specifically engineered to build virtually any width, height, or depth cabinets to 1/16″, one as easy as another.
“Extended stiles” are standard equipment where cabinets meet the walls to avoid the need for ugly and expensive fillers (no extra charge). Appliance and electronic equipment cabinets are manufactured with the right-size openings so no cutting or fitting is needed at the job site (again no extra charge).
Quite unlike “semi-custom” companies with their many surcharges and clumsy, design-restrictive 3″ increments.
“The 3″ increment is dead! Long live the right size!”
Hardwood Corner Blocks
The purpose of corner blocks (sometimes called gussets) is to help keep the cabinet square by bracing against case racking.
“I so love those cabinets and told a couple more people to check out your website.
“I know [my friend] is excited to have you build her cabinets, too. I think she plans to do her kitchen after those bathrooms . . .
“Thank you for all you have done for us.”
— Snohomish, WA
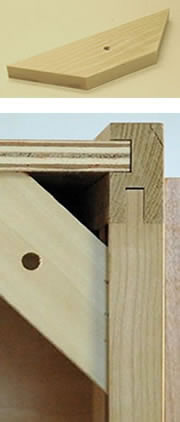
Hardwood Corner Blocks
The purpose of corner blocks (sometimes called gussets) is to help keep the cabinet square by bracing against case racking. When done well, they also enhance the tensile strength of the face frame and end panel joints. Their secondary purpose is to secure the countertop.
Many cabinet companies use molded plastic corner blocks stapled into place through flanges. These have a tendency to break or pull out even before the cabinet is installed, and perform poorly for attaching countertops (some manufacturers even recommend against using them for this purpose). Other companies use weaker particle board or plywood blocks.
Corner block misalignment is a common problem across the industry. Aside from causing squareness issues, misaligned blocks frequently stick up over the top edge of the cabinet and complicate installation and countertop attachment.
Spencer LLC makes and uses premium hardwood corner blocks which are glued and toenailed into a groove, preventing all of these problems. Every cabinet is correct, not just the showroom cabinets. Then we go the extra mile and pre-drill a screw hole so the block won’t split during countertop installation.
Dovetail Drawers
You can usually tell the cabinet quality from a given manufacturer by inspecting drawers they make.
“We love our [entertainment center] and everyone who sees it does as well.
“Thank you again to you and your company for making the unit for us.
“We love it and are getting a lot of use out of it.”
— Everett, WA
Dovetail Drawers
You can usually tell the cabinet quality from a given manufacturer by inspecting drawers they make. Joinery and finish frequently reflect the care, attention to detail, and engineering quality you can expect to see throughout the rest of the cabinet.
First, rub your finger down the joints. It should be smooth without gaps or mismatched parts. A lot of companies leave dovetail ends unfinished and rough, exposing the joinery to water absorption and eventual failure.
Next, note the relative height of the drawer front and side. Many manufacturers leave one higher than the other to accommodate a lack of precision in their processes.
At Spencer LLC, we manufacture all our drawers using tightly-machined dovetail joints for extra strength and dramatic appearance. Both hardwood and plywood drawers are square, smooth and finished, even at the joints. Front, back, and side edges are flush and smooth. We even put an additional coat of varnish on the joints for extra protection against water damage.
Permanent Bumpers
It’s a real shame people spend thousands of dollars for their cabinetry only to end up with cheap “peel and stick” bumper pads.
“Thanks for all your help this past year.
“Love the office! [Attached are] some photos of it . . . .”
— Bothell, WA
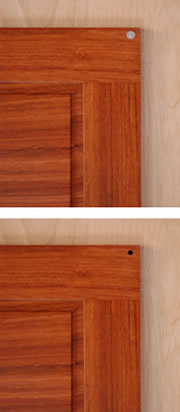
Permanent Door and Drawer Bumpers
If you look in your kitchen or bath cabinets right now, chances are several bumper pads are missing from some of the door and drawer fronts, causing them to bang shut rudely. Some of the remaining bumper pads slid out of position, leaving a sticky trail rather like a snail or slug.
It’s a real shame people spend thousands of dollars for their cabinetry only to end up with cheap “peel and stick” bumper pads which can slide or fall off even in the delivery truck on a sunny day. And they will certainly fall off over time. Tacky.
Spencer LLC only uses soft rubber stem bumpers with integral posts permanently pressed into appropriately drilled holes in the back of the doors or drawer fronts (see photos at the left). We also put them on the backs of false sink fronts and tip-out trays so they are spaced from the cabinet the same as the rest of doors and drawers.
Your doors and drawers always close with a pleasing “fthump”instead of “BANG!” Professional. Clean. Bumpers that can’t fall off. Ever.
Mortise-and-Tenon
Shouldered mortise-and-tenon joinery is the most time-honored method of quality cabinetmaking for some very good reasons:
“I do want to send you a quick note to say we love the entertainment center and using KNK Construction was very helpful. They were great.
“I just have time for a quick note to say thank you for all your help and love your firm’s work.
“I am going to take some pictures and will send some for you to see. We really appreciate your hard work on the center…
“Take good care.”
— Lake Stevens, WA
“P.S. – I have already referred your firm to two people. One for office work and the other for kitchen cabinets.”
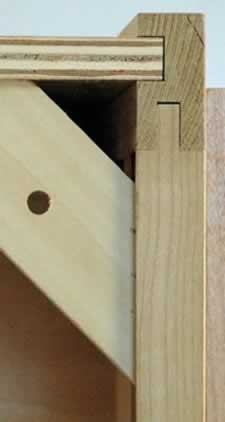
Mortise-and-Tenon Frames & Tongue and Groove Cases
Shouldered mortise-and-tenon joinery is the most time-honored method of quality cabinetmaking for some very good reasons:
Even without glue it forms an extremely strong mechanical joint with superior strength to resist shear, compression, and racking forces. Then add durable glue and a snug fit and its side-grain to side-grain shear resistance is multiplied.
In addition, it cannot twist out of place with “rail spin,” unlike other frames built with crude butt joints and single screws.
The resulting hardwood frame provides a rigid skeleton, providing extra support for the rest of the cabinet, and even the countertop.
Case parts (including the corner blocks) are glued and toe-nailed into grooves for the same long-lived mechanical advantage.
Professional Engineering
Custom details. Wood swelling and shrinking with inevitable humidity changes is one of the more challenging aspects of quality woodworking. And one of the most ignored.
“Thanks for your great work on [my customer’s] kitchen.
“Appliances went in today and she loves everything thus far.
“Dottie, your idea with the shorter side cabinet looks amazing!”
— Sammamish Contractor
Professional Engineering
Wood swelling and shrinking with inevitable humidity changes is one of the more challenging aspects of quality woodworking. And one of the most ignored.
For example, most people (even in the woodworking industry!) don’t realize a solid 24″ wide Maple (or Oak or Hickory, etc.) board is likely to vary up to one-half inch (1/2″) from one season to another. The hydraulic pressures involved can blow apart the most carefully machined and assembled doors and cases unless the certainty of this movement is allowed for.
We run the calculations unique to each wood species to accommodate this wood movement. We make sure the wall cabinet backs and end panels are shear loaded to keep a properly installed cabinet full of your valuable heirloom china securely on the wall, and that the shelves don’t sag. We can also integrate custom features to personalize your cabinets while doing so.
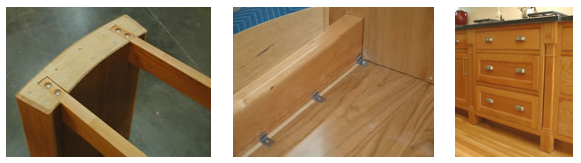
Baked-on Furniture Sheen Finish
There is no secret about our silky smooth finish — the right material applied with the right equipment in the right controlled environment. No dust, no muss!
“We have over 15 years experience in construction, with a large part of that in finish carpentry.
“We have installed thousands of cabinets made by dozens of competitors.
“From the major cabinet companies to the local custom shops, without a doubt we would install Spencer Cabinets in our own homes.”
— Finish Carpenter
Baked On Furniture Sheen Finish
There is no secret about our silky smooth finish — the right material applied with the right equipment in the right controlled environment. No dust, no muss!
Our clean-room finishing and baking system blocks out dust and other contaminants by sealing the process in a rubber-gasketed pressurized chamber, then ventilating it with double-filtered heated air. Other companies’ open booths or paint rooms just don’t “deliver the goods” quite like this system.
First, we hand-wipe your selected stain to bring out the natural wood grain. This technique not only results in the most natural look, it also uses the least material, sparing the outside atmosphere from tons of pollutants a year compared to spray stains typically used by most cabinet manufacturers.
Next, we apply several coats of your choice of a very tough low formaldehyde catalyzed conversion varnish or a formaldehyde-free water-based clear finish. Each coat is baked at exactly the right temperature (up to 175° F) for exactly the right time for a full cure. Different materials require different temperatures and baking times, not the single (or uncontrolled) time and temperature used by other cabinet companies.
Our painted finishes use a “base coat, clear coat” methodology like modern automotive finishes, resulting in a deeper, richer luster.
No secret at all. It’s just nobody else bothers to do it our way.
Glass Paneled Doors
Glass doors for upper cabinets, home theatre installations and bookcases are the trend. Yet most cabinet manufacturers are terrified of breakage with glass doors and, as a result, ship their products with empty frames.
“We have over 15 years experience in construction, with a large part of that in finish carpentry.
“We have installed thousands of cabinets made by dozens of competitors.
“From the major cabinet companies to the local custom shops, without a doubt we would install Spencer Cabinets in our own homes.”
— Finish Carpenter
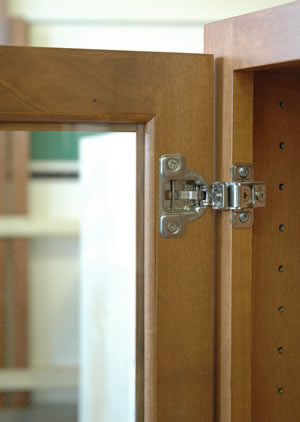
Factory-Installed Glass Paneled Doors
Glass doors for upper cabinets, home theatre installations and bookcases are the trend.
Yet most cabinet manufacturers are terrified of breakage with glass doors and, as a result, ship their products with empty frames.
This widespread practice saddles you with the problem of sourcing, fitting and installing any glass. The resulting quality is dependent entirely on the installer’s glazing skills.
In truth, properly installed glass strengthens and stabilizes the doors, reducing any chance for handling damage. And a professional installation just looks better.
First we shock mount our glass, then we finish the installation with bead moulding made with the same wood species and finish, neatly mitered in the corners.
Unlimited Species
Most stock and semi-custom cabinet manufacturers are limited to four or five species because they have limited room to store all the necessary “standardized” stock parts and panels.
Lumber Parts — Lumber Parts — Choice of Alder, Bamboo, Beech, Yellow Birch, American Cherry, Hickory & Pecan, Eastern White Maple, Red Oak, Quarter Sawn White Oak, Teak, Poplar, and Black Walnut (all FSC). Alder typically has the smallest carbon footprint because it grows locally and abundantly. In addition, it has tremendous finish versatility from rustic to elegant.
Panel Parts — No added urea-formaldehyde (NAUF). Choice of Prefinished Plywood (FSC) or Straw Board (SCS). Matching species veneers use Veneer Plywood (FSC).
Finish — Our use of 100% Hand-Wiped Stain or Natural finishes saves massive amounts of volatile organic compounds (VOCs) from entering the atmosphere compared to spray stains used by most cabinet plants. For the exterior topcoat, we use durable Low Formaldehyde Conversion Varnish, 100% domestically applied.
Packaging — No corrugated paper packaging is used at all. Unlike virtually all other cabinet manufacturers, we deliver our products protected by reusable heavy furniture pads, saving our customers the nuisance and cost of disposing of any cardboard.
Durability — Our “Premium Furniture Construction” combines time-proven joinery with modern finishing techniques.
Heavy, Reusable Furniture Pads
We package our cabinetry using heavy quilted furniture pads instead of corrugated cardboard boxes or face wrapping for the following reasons:
“The closets are absolutely fantastic.
“Thank you so much for taking on this project.
“I am having pitcures professionally taken of the remodel. I will make sure to send you a disk with pictures of both the closets and the vanities.”
— Queen Anne, WA
Heavy, Reusable Furniture Pads
We package our cabinetry using heavy quilted furniture pads instead of corrugated cardboard boxes or face wrapping for the following reasons:
1. Corrugated cardboard is expensive, yet gets thrown right away as waste. Our furniture pads add no cost because they are used over and over again. The money saved goes into cabinetry features you get to keep permanently.
2. Corrugated cardboard is abrasive and can wear through the finish on corners and edges. By contrast, our furniture pads are soft and very protective. Most of our deliveries experience no shipping damage whatsoever.
3. With our furniture pads, you can immediately inspect each and every piece in detail as it arrives. There is no such thing as hidden damage with Spencer cabinets because nothing is hidden.
4. Our furniture pads are returned to our plant to be reused immediately and don’t clutter up the job site. By contrast, corrugated cardboard boxes and packaging used by other companies pile up into a waste disposal problem for you or your contractor, costing you even more time and money. It’s an important side of “green” manufacturing typically passed off as “the customer’s problem.”